Zrozumienie potęgi obróbki elektroerozyjnej drutem
On 8 stycznia, 2022 by admin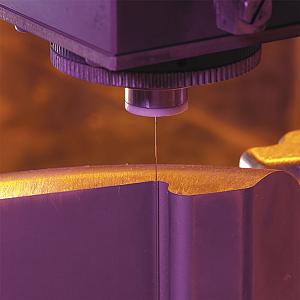
Zdjęcie dzięki uprzejmości Makino.
Obróbka elektroerozyjna drutem (EDM) istnieje od dziesięcioleci, jednak technologia ta nigdy nie przyćmiła innych procesów obróbki na hali produkcyjnej. Dzieje się tak dlatego, że EDM oferuje interesującą propozycję wartości – jest w stanie ciąć każdą część, która jest przewodząca, niezależnie od jej twardości, gdzie konwencjonalne usuwanie metalu jest trudne lub niemożliwe, ale sam proces jest stopniowalny. Eksperci zgadzają się, że sklepy zawsze miały pewne obawy, jeśli chodzi o przyjęcie tej technologii.
„EDM ma piętno czarnej sztuki”, powiedział Brian Pfluger, menedżer linii produktów EDM, Makino, Mason, Ohio. „Sklepy z niewielkim lub żadnym doświadczeniem nie chciały zgłębiać tej technologii, ale ostatnio nastąpiła zmiana.”
„Chociaż EDM drutowa nadal ma niewielki udział w rynku, to zdecydowanie ma swoje miejsce”, powiedział Steve Raucci, menedżer produktu EDM, Methods Machine Tools, Inc. „Aerospace i medycyna to niektóre z sektorów przemysłu, które wdrażają EDM, ale przemysł broni palnej jest kolejnym dużym graczem na rynku EDM. EDM jest powolnym procesem, ale nadal istnieją części, które muszą być produkowane przy użyciu drutu. Czasami nie ma innego sposobu, aby to zrobić.”
Producenci koncentrowali się na tym, jak mały i precyzyjny może być proces EDM. Jednakże, w ciągu ostatnich kilku lat, sam proces osiągnął pewne plateau. Istnieją pewne obszary poprawy. Na przykład, eksperci twierdzili, że jeszcze 10 lat temu, elementy lotnicze o krytycznym znaczeniu dla bezpieczeństwa nigdy nie byłyby produkowane w procesie obróbki elektroerozyjnej. Jednakże, zasilacze i drut zostały przystosowane tak, aby zapewnić, że części mogą być produkowane bez przekuwania i z łatwością z materiałów o różnej grubości.
„Kiedy trzeba wykonać ostre narożniki lub głębokie żebra, cechy, do których konwencjonalne narzędzie frezujące nie może się dostać, drut EDM jest świetną opcją,” powiedział Sean Smith, kierownik sprzedaży – Kanada, GF Machining Solutions, Mississauga, Ont. „Maszyny te są wszechstronne i szczególnie widzimy zapotrzebowanie w obszarach, gdzie materiały stają się coraz twardsze, z wysoką zawartością niklu, co powoduje zwiększony nacisk na narzędzia i wrzeciona. EDM jest idealna do tych zastosowań.”
EDM zdobyła unikalny udział w rynku, i chociaż niektóre cechy uległy plateau, jeden rozwój nastąpił w wielkości obwiedni roboczej.
„Widzimy wzrost wielkości części w branżach, które EDM ma tendencję obsługiwać,” powiedział Evan Syverson, menedżer ds. dodatków i HSM, Sodick Inc, Schaumburg, Ill. „To naprawdę zaczęło wpływać na niektóre specyfikacje i projekty tych maszyn. Powierzchnia podstawy maszyny rośnie w odpowiedzi na typ pracy, który widzimy, szczególnie w osi Z.”
EDMS FOR ADDITIVE MANUFACTURING
Poza tradycyjnymi sektorami, produkcja przyrostowa metali (AM) jest nową szansą rynkową dla EDM. Większość producentów oferuje szeroką gamę maszyn EDM, od podstawowych modeli do maszyn najwyższej klasy z wszystkimi bajerami i gwizdkami. Jednak maszyny zaprojektowane dla metalowych części drukowanych 3D mają bardzo specyficzną funkcję.
„Metalowe części 3D są budowane na płycie bazowej, która musi być usunięta,” wyjaśnił Syverson. „Kiedy część jest drukowana, zazwyczaj ma stosunkowo szeroki skok w osi XY, ale aby usunąć ją z tej płyty, musi być ponownie zorientowana, więc może być ustawiona pionowo i oddzielona za pomocą elektrodrążarki drutowej.”
Te maszyny potrzebują stosunkowo wysokiej osi Z, aby móc pomieścić części i nie muszą być w stanie wykonywać wielu przejść części lub wytwarzać super wysokiej precyzji. EDM dla części drukowanych 3D wymaga ogólnej prędkości i podstawowej zdolności do usunięcia części z płyty bazowej. Więcej producentów koncentruje się na dostarczaniu maszyn zaprojektowanych dla tego segmentu rynku, ponieważ AM staje się coraz bardziej powszechne.
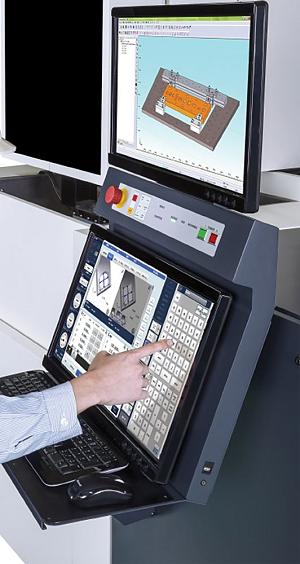
Najnowsze intuicyjne elementy sterujące pozwalają nawet najbardziej niedoświadczonemu operatorowi na dokonywanie bardzo precyzyjnych, eksperckich regulacji maszyny bez konieczności znajomości podstawowej technologii. Zdjęcie dzięki uprzejmości firmy Makino.
GETTING CONTROL
Producenci tej technologii dostosowali system tak, aby był łatwy w użyciu, rozwiewając pogląd, że obróbka elektroerozyjna jest pewnego rodzaju „czarną magią”, którą mogą obsługiwać tylko eksperci w tej dziedzinie.
„Unowocześnienie systemów sterowania pomogło wyeliminować strach przed nieznanym, kiedy operatorzy nie chcą naciskać niewłaściwych przycisków lub nie rozumieją, jak współpracować z maszyną,” powiedział Pfluger.
Najnowsze intuicyjne systemy sterowania pozwalają nawet najbardziej niedoświadczonemu operatorowi dokonywać bardzo precyzyjnych, eksperckich regulacji maszyny bez konieczności znajomości technologii, która leży u jej podstaw. Graficzne interfejsy, które zapewniają liczne adaptacyjne elementy sterujące, ułatwiają operatorowi dostosowanie parametrów do wykonywanej pracy. Jest to szczególnie ważne, ponieważ często wyzwaniem może być znalezienie wykwalifikowanych operatorów, którzy mają wcześniejsze doświadczenie w obróbce elektroerozyjnej.
„Sterowanie i technologia stały się prostsze i łatwiejsze w obsłudze niż 10 lat temu,” powiedział Raucci. „Interfejs pozwala operatorowi wybrać średnicę drutu, grubość materiału itd. Maszyna obliczy parametry cięcia potrzebne do wykonania zadania.” Raucci dodał, że jest to znacząca poprawa w ciągu ostatnich kilku lat. Kiedy zaczynał pracę w branży, parametry cięcia znajdowały się w podręcznikach, a jeśli to, czego szukał operator, nie było w nich uwzględnione, musiałby bawić się specyfikacją, aby uzyskać odpowiednie opcje.
„Teraz wszystko, co naprawdę musisz wiedzieć, to rozmiar obrabianego przedmiotu, tolerancja, jakiej szukasz, jakość powierzchni, jaką próbujesz osiągnąć, wraz z wybranym drutem” – powiedział Smith. „Teraz to już proste, jak wypełnienie pustych pól na panelu sterowania. Maszyna przejmuje kontrolę.”
Maszyny są również wyposażone w funkcje pomagające w zwiększeniu wydajności. Producenci zauważyli, że dodanie trybu ekonomicznego lub opcji oszczędzania energii jest korzystne dla użytkowników, którzy obsługują maszynę przy zgaszonym świetle.
Smith podaje przykład wykonywania pracy w weekend, gdzie nie ma pośpiechu, aby część została ukończona tak szybko, jak to możliwe. Funkcje takie jak tryb ekonomiczny zmniejszą parametry pracy, oszczędzając przewód i zużycie energii. Zamiast więc mieć część ukończoną w sobotę po południu przy pełnych kosztach operacyjnych, można ją ukończyć kilka godzin później, korzystając z maszyny pracującej w trybie oszczędzania energii.
PRZEWÓD
„Jedną z największych innowacji na rynku jest obecnie możliwość przewlekania drutu w szczelinie” – powiedział Pfluger. W przypadku pęknięcia drutu, co może się zdarzyć, taka możliwość pozwala na ponowne nawleczenie drutu w miejscu pęknięcia, zamiast cofania się do początku.
„Prawie nie można by prowadzić operacji z wyłączonym światłem, gdyby nie było systemu wykrywania pęknięć” – powiedział Syverson.
Producenci koncentrują się na opracowywaniu zaawansowanych nawlekarek drutu, które zwiększają wydajność, oferują lepszą niezawodność i usprawniają przetwarzanie części. Posiadanie systemu, który wykrywa również zerwanie drutu i ostrzega operatora, ułatwia przywrócenie maszyny do wydajnej pracy.
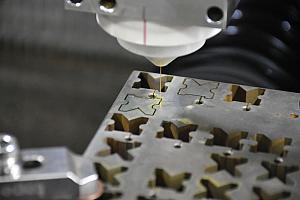
Utrzymywanie ślimaków zapobiega ich spadaniu i eliminuje potrzebę stosowania zacisków. Automatyczny system podawania drutu może przewlec drut przez krawędź, co pozwala na pełne wykorzystanie tej funkcji. Zdjęcie dzięki uprzejmości firmy Methods Machine Tools.
Gwintownice drutu i systemy wykrywania pęknięć są ważnymi komponentami, ale Pfluger wyjaśnił, że jednym z największych kosztów eksploatacji maszyny, oprócz opłacenia operatora obsługującego maszynę, jest sam drut. Coraz więcej producentów koncentruje się na opracowywaniu bardziej wydajnych ustawień maszyn, które zużywają mniej drutu przy zachowaniu jakości części.
Spowodowało to, że wielu producentów oferuje obecnie technologię drutu o dużej średnicy. Na przykład, Pfluger wyjaśnił, że najbardziej powszechny drut ma średnicę 0,25 mm, ale coraz więcej operatorów stosuje drut o większej średnicy, na przykład drut o średnicy 0,3 mm, ponieważ oferuje on korzyści związane z prędkością. Ogólnie rzecz biorąc, im szybciej pracuje maszyna, tym bardziej operator musi poświęcić jakość wykończenia i dokładność tradycyjnych rozmiarów drutu, stosując drut o większej średnicy. Jednakże, producenci opracowują zoptymalizowane ustawienia maszyny, które zapewniają takie samo wykończenie powierzchni i dokładność przy zastosowaniu drutu o większej średnicy, jak w przypadku drutu tradycyjnego. Pozwala to na zaoszczędzenie do 20% czasu cyklu, szczególnie w przypadku cięć zgrubnych. Obniża to również zużycie drutu, co prowadzi do znacznych oszczędności kosztów.
Operacje WYŁĄCZONE
Wire EDM ma pewne wbudowane ograniczenia i zmienne maszynowe, które sprawiają, że jest trudna do zautomatyzowania, dlatego też robotyzacja nigdy nie była powszechnym trendem w tej technologii. Ale eksperci są zgodni, że coraz więcej klientów pyta o sposoby automatyzacji procesu.
„Widzimy coraz więcej komórek EDM z wyspecjalizowaną automatyką”, powiedział Raucci. „Dziesięć lat temu nic takiego nie istniało. Komórki mają tendencję do posiadania wielu maszyn EDM z automatyką systemu szynowego. Ten trend staje się coraz bardziej popularny ze względu na zwiększone koszty pracy i brak wykwalifikowanych operatorów.”
Raucci zauważył, że nadal istnieje duży podział w tym, czego szukają klienci. Powiedział, że niektórzy lubią standardowe maszyny z jednym operatorem, podczas gdy inni wskakują z pełnymi możliwościami wyłączania świateł. Może to obejmować stół obrotowy z dodatkową automatyką i sondą. Wbudowanie sondy zapewnia jakość części, co może być niezwykle korzystne dla każdego, kto chce prowadzić operacje bezświatłowe.
„Dodanie automatyzacji to zdecydowanie sposób, w jaki klienci mogą być bardziej konkurencyjni na rynku”, dodał Smith. „Mogą oni przejść od bardzo podstawowego systemu zmieniacza palet aż do wieloosiowych robotów, które pomagają załadować maszyny.”
Eksperci zgodzili się, że automatyzacja i operacje typu lights-out ułatwiają sklepom wejście w tę technologię. Jednak Smith ostrzegł, że sklepy, które chcą wprowadzić zrobotyzowaną komórkę, muszą również zapewnić sobie wystarczającą ilość przewodów, aby w pełni wykorzystać tę technologię. W przeważającej części, dzisiejsze maszyny mogą pomieścić około 55 funtów drutu, co daje około 80 godzin czasu cięcia bez nadzoru i energii.
„Technologia sama w sobie przeszła tak długą drogę na przestrzeni lat,” powiedział Syverson. „Jeżeli operator potrafi korzystać z elementów sterujących i oprogramowania pokładowego, maszyna w zasadzie pracuje sama. A teraz, dzięki automatyzacji, jest więcej sposobów niż kiedykolwiek, aby sklepy mogły skorzystać z unikalnych możliwości EDM.”
Associate Editor Lindsay Luminoso można uzyskać pod adresem [email protected].
GF Machining Solutions, www.gfms.com
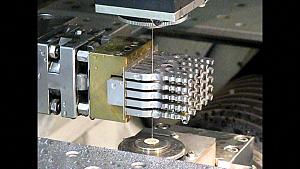
„Jednym z wielkich impulsów na rynku jest obecnie możliwość nawlekania drutu w szczelinie,” powiedział Brian Pfluger. Zdjęcie dzięki uprzejmości Makino.
Makino, www.makino.com
Methods Machine Tools, www.methodsmachine.com
Sodick, www.sodick.com
Dodaj komentarz