Wat is een pFMEA? (d.w.z., proces Failure Mode and Effect Analysis) Medical Device Academy
On januari 4, 2022 by adminWat is een pFMEA? (d.w.z. proces Failure Mode and Effect Analysis)
Geplaatst door Matthew Walker op 6 september 2019
In dit artikel wordt uitgelegd wat een pFMEA is (d.w.z. proces Failure Modes and Effects Analysis) en hoe u deze kunt gebruiken als onderdeel van uw risicobeheerproces.
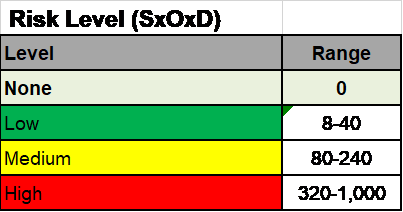
Ik had onlangs iemand die om hulp vroeg om de proces Failure Mode and Effect Analysis (pFMEA) wat beter te begrijpen. Ik kan het hem niet kwalijk nemen, want ik was de eerste keer dat ik een formulier probeerde in te vullen de weg kwijt. Het kan verwarrend en overweldigend zijn als je er nog nooit een hebt gemaakt.
Vorige dingen eerst, wat is een pFMEA
FMEA= Failure Modes and Effects Analysis
Er komt een kleine letter voor de FMEA, en dat geeft het ‘wat’ aan, van wat de storing is die wordt geanalyseerd. Een pFMEA zal vaak processtoringen onderzoeken, terwijl een dFMEA ontwerpstoringen kan evalueren. (dFMEA’s kunnen ook verwarrend zijn, Robert Packard heeft in zijn Death of the dFMEA Webinar een training gegeven over hoe je risicomanagement activiteiten kunt documenteren zonder er een te gebruiken)
Sommige systemen geven alle letters een hoofdletter. Sommige geen. Dat is niet belangrijk, zolang het maar consistent is in uw hele systeem. Iedereen moet gemakkelijk kunnen begrijpen dat welke variatie van pfmea ook wordt gebruikt; het betekent “process failure modes and effects analysis”.
Wat doet een pFMEA?
Een pFMEA splitst uw productieproces op in de afzonderlijke stappen en onderzoekt deze methodisch op potentiële risico’s of storingen. Voor bedrijven die gebruik maken van ons Turn-Key Quality Management System, kan FRM-025 proces Failure Modes, and Effects Analysis worden gebruikt als sjabloon.
In dit voorbeeld bekijken we de ontvangstinspectie van spuitgegoten behuizingsonderdelen voor een medisch hulpmiddel. Deze ontvangstinspectie omvat een handmatige inspectie van 10 willekeurig geselecteerde onderdelen uit elke levering van 100 met behulp van een optische overlay.
Processtap
Dit gebied is, zoals de titel van het hoofdstuk al aangeeft, de processtap. Wanneer naar het proces als geheel wordt gekeken, wordt het in de pFMEA uitgesplitst in elke afzonderlijke stap in dat proces. Dit gebied is eenvoudigweg die afzonderlijke stap die zal worden onderzocht.
De processtap of itemfunctie, afhankelijk van wat uw formulier gebruikt voor dit scenario, zal deel uitmaken van de steekproef voor handmatige inspectie van de ontvangen onderdelen met behulp van een optische overlay. Ons voorbeeld zal het achtergrondverlichtingselement van het optische overlaydisplay zijn. Het achtergrondverlichtingselement zal het geïnspecteerde onderdeel tegen het sjabloon verlichten om te verifiëren of het onderdeel binnen specifieke maatcriteria valt.
Potentiële faalwijzen
Een faalwijze is een manier waarop die processtap zou kunnen falen. Aangezien het om failure modeS gaat, moet er rekening mee worden gehouden dat de processtap op meer dan één manier kan falen. Laat u niet wijsmaken dat omdat dit vakje op het formulier is ingevuld, de pFMEA compleet zal zijn. Alle mogelijke mislukkingen moeten grondig worden onderzocht.
Ons voorbeeld in dit proces vereist dat het achtergrondverlichtingselement een visueel sjabloon over de onderdelen verlicht. Het niet goed oplichten van het licht is een mogelijke foutmodus van dit proces.
Potentiële gevolgen van falen
de potentiële gevolgen van het falen is een blik op wat de gevolgen zouden zijn als dat falen voor die processtap werkelijk zou gebeuren.
In ons scenario is een van de mogelijke gevolgen van het niet goed functioneren van de verlichting, dat onderdelen die buiten de aangewezen acceptatiecriteria voor de dimensionering vallen, worden geaccepteerd in plaats van afgekeurd als niet-conforme onderdelen.
S (Ernst)
Het volgende gebied is het eerste gebied waarvoor een schatting van de ernst van de storing nodig is. Dat is ‘Severity’, afgekort als S. Er is een schaal in de beoordelingssectie van FRM-025 die het nummeringssysteem schetst dat Medical Device Academy gebruikt.
Hieronder vindt u een uittreksel van de gebruikte beoordelingsschaal, die wordt meegeleverd bij de aanschaf van de SYS-010 Risk Management Procedure.
Seurnity (S) | ||
Ernst van het effect | Scale | Definition |
Bedrijfsrisico | 0 | Geen potentiële schade voor patiënt of gebruiker |
Oppervlakkig | 2 | Weinig potentieel voor schade voor patiënt of gebruiker |
In dit geval, gebruiken we in dit geval gegoten plastic stukjes van de buitenmantel van een medisch hulpmiddel. Te grote of te kleine stukken passen niet bij de uiteindelijke assemblage van het hulpmiddel. Deze plastic stukken komen niet in aanraking met de patiënt en hebben geen invloed op de werking van het hulpmiddel.
Bij de evaluatie van dit defect is vastgesteld dat het geen potentieel effect heeft op de veiligheid van de patiënt en geen potentieel risico op schade verhoogt; daarom wordt de ernst ervan aangemerkt als een “bedrijfsrisico”, wat betekent dat het geen risico inhoudt voor de gebruiker of de patiënt. Dit maakt de ernstscore 0.
Oorzaken van het falen
Deze kolom is precies dat. Wat kan de oorzaak zijn van deze vastgestelde fout? In ons voorbeeld zouden de gloeilampen in de overlay machine na verloop van tijd door het gebruik langzaam kunnen doorbranden. Dit doorbranden veroorzaakt een mogelijke storing.
Als de gloeilamp naar verwachting slechts 100 uur meegaat, dan kan het licht zwakker worden naarmate de lamp meer uren wordt gebruikt. Een langzaam dimmend licht vermindert de scherpte van het overlaysjabloon en onze onderdelen die verondersteld worden een + of – maatcriteria van 10% te hebben, hebben nu een vaag sjabloon dat in werkelijkheid het overlaysjabloon verandert om dichter bij + of – 13% aan te geven. Nu kunnen onderdelen die te klein of te groot zijn worden geaccepteerd.
O (Occurrence/Probability)
Dit sorteringscriterium is ook te vinden in de Rating-sectie van FRM-025. Dit is hoe vaak de storing zich naar verwachting zal voordoen. Hoe vaak zal het verlichtingselement van onze optische overlay niet naar behoren functioneren voor deze oorzaak?
Hopelijkerwijs niet erg vaak. Regelmatig gepland onderhoud en ijking van de overlaymachine kunnen in het beste geval zelfs voorkomen dat dit ooit gebeurt. Onze evaluaties wijzen uit dat de kans dat dit gebeurt, gering is. Maar omdat we er niet zeker van kunnen zijn dat het nooit zal gebeuren, bestaat de kans op dit risico en is de score voor deze gebeurtenis een 4.
Huidige procesbeheersingsmaatregelen
Wat wordt er momenteel gedaan om dit risico te beheersen? In ons voorbeeld wordt gebruikgemaakt van regelmatig gepland onderhoud en kalibratie om te voorkomen dat de lamp doorbrandt en de overlay wordt aangetast.
D (Detecteerbaarheid)
Onze huidige werkwijze is gebaseerd op periodiek onderhoud en visuele inspectie. Dit betekent dat het doorbranden van de lamp iets is dat visueel wordt geïnspecteerd en dat de visuele inspecties voor detecteerbaarheid op de beoordelingsschaal worden gerangschikt als 8. Deze grafiek is te vinden in de beoordelingssectie van FRM-025.
RPN (Risk Priority Number)
Dit is een getal dat wordt verkregen door de ernst te vermenigvuldigen met de waarschijnlijkheid en de detecteerbaarheid. In ons voorbeeld is het getal RPN 0X4X8=32 voor een RPN van 32 dat als LAAG wordt beschouwd.
pFMEA-wiskunde
Hieronder vindt u een korte video waarin de wiskunde achter de berekening van het Risicoprioriteitennummer wordt uitgelegd
Aanbevolen acties
Wat kan er eventueel nog worden gedaan om dit proces te verbeteren? In ons voorbeeld kan een aanbevolen actie zijn om over te schakelen van inspecties die alleen visueel zijn, naar verificatie van de lichtopbrengst door de meter. Dit maakt de detecteerbaarheid van de fout meetbaar door meter of gage wat een detecteerbaarheidsscore van 4 is.
Dit verandert de RPN nu in 0X4X4=16
De pFMEA zou geen solo-ding moeten zijn
Als het vermeden kan worden zou dit type analyse gedaan moeten worden door een multidisciplinair team. Soms moeten mensen in kleinere bedrijven meer dan één pet dragen. Er zijn veel ondernemers die moeten fungeren als CEO/CFO/Design Engineer/RA/QA manager.
In principe moet een teamaanpak worden gebruikt als dat haalbaar is. Laat het personeel op managementniveau, dat eigenaar is van de processen, deelnemen aan deze analyse. Zij zouden het proces beter moeten kennen dan wie ook in het bedrijf en meer inzicht moeten hebben in de mogelijke faalwijzen van de processen, omdat zij die waarschijnlijk uit de eerste hand hebben gezien. Zij zijn ook het soort werknemers dat de aanbevolen maatregelen zou kennen om het risico van die storingen te beheersen.
De pFMEA moet ook een levend document zijn
Als nieuwe faalwijzen worden ontdekt, moeten ze aan uw pFMEA worden toegevoegd. Een nieuwe foutmodus kan worden ontdekt via een CAPA, omdat het proces een feitelijke fout vertoonde die oorspronkelijk niet was geanalyseerd. Gebruik zo’n geval als een kans voor verbetering en om uw pFMEA bij te werken als onderdeel van een levend risicobeheersysteem. Gebruik dit ook als een moment om opnieuw te brainstormen over mogelijk vergelijkbare faalwijzen die misschien niet eerder zijn overwogen, zodat ze kunnen worden beheerst voordat ze zich voordoen.
Als u de tijd heeft genomen om de video hierboven te bekijken, wordt ook vermeld dat in sommige gevallen de allereerste FMEA gebaseerd moet zijn op schattingen, omdat er geen gegevens zijn. Managers en ingenieurs kunnen gedwongen zijn om de waarschijnlijkheid van optreden in te schatten. Als dat het geval is, moet de FMEA in de toekomst worden bijgewerkt om de (O) score aan te passen aan wat er in werkelijkheid gebeurt, gebaseerd op echte gegevens en niet op de theoretische gegevens die werden gebruikt voor de eerste schatting.
Geef een antwoord