pFMEAとは何ですか? (i.e., process Failure Mode and Effect Analysis) 医療機器アカデミー
On 1月 4, 2022 by adminpFMEA とは何ですか? (i.e., process Failure Mode and Effect Analysis)
Posted by Matthew Walker on September 6, 2019
この記事では、pFMEAとは何か(すなわちProcess Failure Modes and Effects Analysis)、リスク管理プロセスの一部としてどのように使用するかを説明します
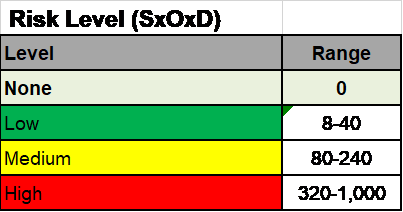
私は最近ある人に、プロセス故障モードおよび影響解析(pFMEA)をもう少し理解したいとの依頼がありました。 私も初めてフォームに記入しようとしたときに迷ったので、彼らを責めることはできません。 初めて作成する場合は、混乱し、圧倒されるかもしれません。
First things first, what is a pFMEA
FMEA=Failure Modes and Effects Analysis
FMEA の前に小文字がありますが、これは「何を」、つまり分析対象の故障が何であるかを示しているのです。 pFMEAではプロセスの故障を調べることが多く、dFMEAでは設計の故障を評価することがある。 (dFMEAは混乱することもあり、Robert Packardは彼のDeath of the dFMEA Webinarで、dFMEAを使用せずにリスクマネジメント活動を文書化する方法についてのトレーニングを行いました)
システムによっては、すべての文字を大文字にするものもあります。 あるものは、何も大文字にしません。 それは、システム全体で一貫している限り、重要なことではありません。 pfmeaのどのようなバリエーションが使用されていても、それは「プロセスの故障モードと影響解析」を意味することを誰もが簡単に理解できるようになるはずです。
pFMEA では何をするのですか。
pFMEA では、製造プロセスを個々のステップに分解し、潜在的なリスクや故障がないかどうかを系統的に調査します。 当社のターンキー品質管理システムを利用する企業では、FRM-025プロセスの故障モードおよび影響解析がテンプレートとして使用されることがあります。
この例では、医療機器用の射出成形されたケーシング部品の受入検査について見てみましょう。 この受入検査では、光学オーバーレイを使用して、各出荷100個のうちランダムに選択した10個の部品を手作業で検査します。
Process Step
この領域は、セクションのタイトルが示すように、プロセスステップである。 プロセスを全体として見る場合、pFMEAでは、そのプロセスに含まれる一つ一つのステップに分解していきます。
プロセスステップまたはアイテム機能は、このシナリオのために使用するフォームに応じて、光学オーバーレイを使用して受信した部品の手動検査のためのランダムサンプリングの一部となる予定である。 この例では、光学オーバーレイディスプレイのバックライト要素を使用する予定です。 バックライトは、検査された部品をテンプレートに照らして、その部品が特定の寸法基準内にあることを確認するために使用されます。
Potential Failure Modes
故障モードとは、そのプロセス手順が失敗する可能性のある方法を指します。 故障モードSなので、そのプロセスステップが故障する方法は1つではない可能性があることを考慮する必要がある。 この欄が埋まったからpFMEAが完了したと侮るなかれ。 起こりうるすべての失敗を徹底的に調べるべきである。
このプロセスの例では、部品の上に視覚的なテンプレートを照らすために、バックライト要素が必要です。 ライトが適切に照らされないことは、このプロセスの潜在的な故障モードです。
失敗の潜在的影響
失敗の潜在的影響とは、そのプロセスステップの失敗が実際に起こった場合、どのような影響があるのかを調べることです。
このシナリオでは、照明が正しく機能しないことによる潜在的な影響の1つとして、指定されたサイズ許容基準外の部品が、不適合部品として拒否されるのではなく、受け入れられる可能性があることを挙げています。
S (Severity)
次の領域は、故障の推定等級付けを必要とする最初の領域です。 FRM-025の評価セクションには、Medical Device Academyが使用する番号付けシステムの概要を示す尺度が用意されています。
以下は、使用されている評価スケールの一部です。これは、SYS-010リスク管理手順の購入時に同梱されています。
重大度 (S) | ||
影響の重大さ | スケール | 定義 |
ビジネスリスク | 0 | 患者やユーザーに害を与える可能性はない |
Superficial | 患者やユーザーに害を与える可能性は少ない |
この場合、以下のようになります。 この例では、医療機器の外側のケーシングのプラスチック成形品を使用しています。 大きすぎたり小さすぎたりする部品は、機器の最終的な組み立てを行う際にフィットしません。 これらのプラスチック片は、患者に接触することはなく、装置の機能には影響しません。
この不具合の評価は、患者の安全性に影響を与える可能性はなく、危害のリスクの可能性を高めることもないと判断されたため、重大度は、ユーザーや患者にとってリスクをもたらさないという意味の「ビジネスリスク」として割り当てられています。
Causes of Failure
この欄はまさにそれです。 この特定された障害が起こる原因は何でしょうか。 この例では、オーバーレイマシンの電球が、使用するうちに徐々に焼き切れる可能性があります。 この焼きつきは潜在的な故障の原因となります。
電球の寿命が 100 時間しかないと予想される場合、使用時間が長くなればなるほど、光は弱くなる可能性があります。 徐々に暗くなる光は、オーバーレイ テンプレートの鮮明さを低下させ、10% の + または – サイズ基準を持つはずのパーツが、実際には + または – 13% に近い表示にオーバーレイを変更するあいまいなテンプレートになってしまいます。 これで、小さすぎたり大きすぎたりするパーツも受け入れられるようになりました。
O (発生/確率)
この評価基準は FRM-025 の評価のセクションにも記載されています。 これは、その故障がどのくらいの頻度で発生すると予想されるかを示しています。 当社の光学オーバーレイの照明要素が、この原因に対して適切な方法で機能しないことがどれくらいの頻度で起こるでしょうか。 実際、オーバーレイマシンの定期的なメンテナンスとキャリブレーションにより、最良のシナリオであれば、このようなことが起こるのを防ぐことができます。 私たちの評価では、この現象が起こる確率は低いと判断しています。 しかし、絶対に起こらないとは言い切れないため、このリスクの可能性は存在し、発生スコアは4となります。
Current Process Controls
このリスクを制御するために現在何が行われていますか。 この例では、オーバーレイに影響を与える電球の焼損を防ぐために、定期的なメンテナンスと校正を行っています。
D (検出可能性)
私たちの現在のプロセスは、定期的なメンテナンスと目視検査に基づくものです。 これは、電球の焼損は目視で検査されるものであり、評価スケールの検出性の目視検査は8として評価されることを意味します。このチャートは、FRM-025の評価セクションにあります。
RPN (Risk Priority Number)
これはSeverityとProbabilityとDetectabilityを掛け合わせた数字です。 この例では、RPNは0X4X8=32で、RPNは32となり、LOWとみなされます。
pFMEA math
以下は、リスク優先順位番号の計算の背後にある数学を説明する短いビデオです
Recommended Action
このプロセスを改善できるものがあるとしたら何でしょうか。 この例では、目視のみの検査から、メーターによる光出力の確認に移行することが推奨されます。
これにより、RPN は 0X4X4=16
The pFMEA should not be a solo thing
If it can avoid this type of analysis should be done by a multidisciplinary team.これは、故障の検出性をメーターまたはゲージで測定できるようにするためのもので、検出性スコアは 4 です。 小さな会社では、複数の帽子をかぶらなければならないことがあります。 CEO/CFO/設計エンジニア/RA/QAマネージャーとして機能しなければならない起業家がたくさんいます。
可能であれば、チームアプローチを用いるのが理想的です。 プロセスのオーナーシップを持つ管理レベルのスタッフにこの分析に参加させるのです。 彼らは社内の誰よりも親密にプロセスを知っているはずであり、プロセスの起こりうる故障モードを直接見てきた可能性が高いため、より深い洞察力を持つはずです。 また、そのような故障のリスクをコントロールするために推奨されるアクションの種類も知っているタイプの従業員です。
また、pFMEAは生きた文書であるべきです
新しい故障モードが発見されたら、それらはpFMEAに追加されるべきです。 新しい故障モードは、もともと分析されていなかったプロセスで実際に故障が発生したため、CAPAを通じて発見されるかもしれません。 このような事例は、改善の機会ととらえ、リスクマネジメントシステムの一部として、pFMEAを更新することが必要です。 また、この機会に、以前は考慮されていなかった類似の故障モードを再度検討し、発生する前に制御できるようにしましょう。
上記のビデオをご覧になった方は、データがないため、最初の FMEA は推定に基づかなければならない場合があることにも言及されています。 マネージャーやエンジニアは、発生確率を推定せざるを得ないかもしれません。 その場合、FMEAは将来更新され、最初の見積もりに使われた理論的なデータではなく、実際のデータに基づいて実際に発生していることを反映するように(O)スコアを調整しなければなりません。
コメントを残す