¿Qué es un pFMEA? (es decir, análisis de modo de fallo y efecto del proceso) Medical Device Academy
On enero 4, 2022 by admin¿Qué es un pFMEA? (i.e., process Failure Mode and Effect Analysis)
Posted by Matthew Walker on September 6, 2019
Este artículo explica qué es un pFMEA (i.e. Process Failure Modes and Effects Analysis) y cómo utilizarlos como parte de su proceso de gestión de riesgos.
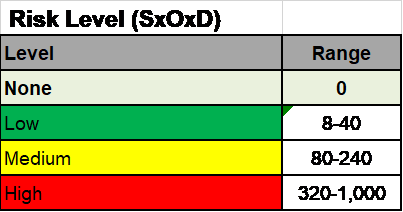
Recientemente alguien me pidió ayuda para entender un poco mejor el Process Failure Mode and Effect Analysis (pFMEA). No puedo culparles, porque yo me perdí la primera vez que intenté rellenar un formulario para uno. Puede ser confuso y abrumador si nunca has creado uno antes.
Primero lo primero, qué es un pFMEA
FMEA= Análisis de Modos de Fallo y Efectos
Una letra minúscula vendrá antes del FMEA, y eso denota el ‘qué’, de cuál es el fallo que se está analizando. Un pFMEA a menudo examinará los fallos del proceso, mientras que un dFMEA podría evaluar los fallos del diseño. (Los dFMEA también pueden ser confusos, Robert Packard creó una formación sobre cómo documentar las actividades de gestión de riesgos sin utilizar uno en su Webinar Death of the dFMEA)
Algunos sistemas ponen todas las letras en mayúscula. Otros no ponen ninguna en mayúscula. Eso no es lo importante siempre que sea consistente en todo su sistema. Todo el mundo debería ser capaz de entender fácilmente que cualquiera que sea la variación de pfmea que se utilice; significa «análisis de modos de fallo y efectos del proceso.»
¿Qué hace un pFMEA?
Un pFMEA desglosará su proceso de fabricación en sus pasos individuales y los examinará metódicamente en busca de riesgos o fallos potenciales. Para las empresas que utilizan nuestro sistema de gestión de calidad «llave en mano», se puede utilizar como plantilla el proceso FRM-025 de análisis de fallos y efectos.
Para este ejemplo, veremos la inspección de recepción de piezas de carcasa moldeadas por inyección para un dispositivo médico. Esta inspección de recepción incluye una inspección manual de 10 piezas seleccionadas al azar de cada entrega de 100 utilizando una superposición óptica.
Paso del proceso
Esta área, como sugiere el título de la sección, es el paso del proceso. Al mirar el proceso como un todo, el pFMEA lo desglosará en todos y cada uno de los pasos incluidos en ese proceso. Esta área es simplemente ese paso individual que va a ser examinado.
El paso del proceso o la función del elemento, dependiendo de lo que su forma utiliza para este escenario, va a ser parte del muestreo aleatorio para la inspección manual de las piezas recibidas utilizando una superposición óptica. Nuestro ejemplo va a ser el elemento de retroiluminación de la pantalla de superposición óptica. El elemento de retroiluminación iluminará la pieza inspeccionada contra la plantilla para verificar que la pieza está dentro de los criterios de dimensión específicos.
Modos de fallo potenciales
Un modo de fallo es una forma en la que ese paso del proceso podría fallar. Dado que se trata de un modo de falloS, hay que tener en cuenta que puede haber más de una forma de que el paso del proceso falle. No se engañe pensando que porque se haya rellenado esta casilla del formulario el AMFE estará completo. Debe investigarse un examen exhaustivo de todos los posibles fallos.
Nuestro ejemplo en este proceso requiere que el elemento de retroiluminación ilumine una plantilla visual sobre las piezas. Que la luz no ilumine correctamente es un modo de fallo potencial de este proceso.
Efectos potenciales del fallo
Los efectos potenciales del fallo es una mirada a lo que serían las ramificaciones si ese fallo para ese paso del proceso ocurriera realmente.
En nuestro escenario, uno de los efectos potenciales de que la iluminación no funcione correctamente es que las piezas fuera de los criterios de aceptación de tamaño designados pueden ser aceptadas en lugar de ser rechazadas como piezas no conformes.
S (Severidad)
La siguiente área es la primera que requiere una clasificación estimada del fallo. Se trata de la ‘Severidad’, que se abrevia como S. Hay una escala proporcionada en la sección de calificación del FRM-025 que describe el sistema de numeración que utiliza la Academia de Dispositivos Médicos.
A continuación se muestra un fragmento de la escala de clasificación utilizada, que se incluye con la compra del Procedimiento de Gestión de Riesgos SYS-010.
Severidad (S) | ||
Severidad del efecto | Escala | Definición |
Riesgo empresarial | 0 | Ningún daño potencial para el paciente o el usuario |
Superficial | 2 | Poco potencial de daño para el paciente o el usuario |
En este caso, nuestro ejemplo es utilizar piezas de plástico moldeadas de la carcasa exterior de un dispositivo médico. Las piezas demasiado grandes o demasiado pequeñas no encajarán al hacer el montaje final del dispositivo. Estas piezas de plástico no pasan a estar en contacto con el paciente, y no afectan al funcionamiento del dispositivo.
La evaluación de este fallo se determina que no tiene ningún efecto potencial sobre la seguridad del paciente ni aumenta ningún riesgo potencial de daño, por lo que la gravedad se asigna como «riesgo comercial», lo que significa que no conlleva ningún riesgo para el usuario o el paciente. Esto hace que la puntuación de gravedad sea 0.
Causas del fallo
Esta columna es exactamente eso. ¿Qué puede causar este fallo identificado? En nuestro ejemplo podrían ser las bombillas de la máquina de superposición pueden quemarse lentamente con el tiempo con el uso. Este agotamiento provoca un fallo potencial.
Si se espera que la bombilla tenga una vida útil de sólo 100 horas, entonces cuantas más horas se utilice la bombilla, más se atenuará la luz. Una luz que se atenúa lentamente disminuye la nitidez de la plantilla de superposición y nuestras piezas que se supone que tienen un criterio de tamaño de + o – 10% ahora tienen una plantilla borrosa que en realidad cambia la superposición para mostrar más cerca de + o – 13%. Ahora las partes que son demasiado pequeñas o demasiado grandes pueden ser aceptadas.
O (Ocurrencia/Probabilidad)
Este criterio de calificación también se encuentra en la sección de Calificación del FRM-025. Se trata de la frecuencia con la que se espera que se produzca el fallo. ¿Con qué frecuencia dejará de funcionar el elemento de iluminación de nuestra superposición óptica de la manera adecuada para esta causa?
Es de esperar que no sea muy frecuente. De hecho, el mantenimiento y la calibración programados con regularidad de la máquina de superposición podrían evitar que esto ocurra en el mejor de los casos. Nuestras evaluaciones determinan que la probabilidad de que esto ocurra es baja. Sin embargo, dado que no podemos estar seguros de que nunca ocurrirá, el potencial de este riesgo existe y hace que la puntuación de Ocurrencia sea un 4.
Controles actuales del proceso
¿Qué se está haciendo actualmente para controlar este riesgo? Nuestro ejemplo utiliza el mantenimiento y la calibración programados regularmente para evitar que la quemadura de la bombilla afecte a la superposición.
D (Detectabilidad)
Nuestro proceso actual se basa en el mantenimiento rutinario y la inspección visual. Esto significa que la quemadura de la bombilla es algo que se inspecciona visualmente y las inspecciones visuales para la detectabilidad en la escala de calificación se califican como 8. Esta tabla se encuentra en la sección de calificación de FRM-025.
RPN (Número de Prioridad de Riesgo)
Este es un número que se encuentra multiplicando la Severidad, por la Probabilidad, por la Detectabilidad. En nuestro ejemplo, los números RPN son 0X4X8=32 para un RPN de 32 que se considera BAJO.
Matemáticas del PFMEA
A continuación se muestra un breve vídeo en el que se explican las matemáticas que hay detrás del cálculo del Número de Prioridad de Riesgo
Acciones recomendadas
¿Qué se puede hacer para mejorar este proceso? En nuestro ejemplo, una acción recomendada puede ser pasar de las inspecciones sólo visuales a la verificación de la salida de luz por el medidor. Esto hace que la detectabilidad del fallo sea medible por el medidor o calibrador, lo que supone una puntuación de detectabilidad de 4.
Esto cambia el RPN ahora a 0X4X4=16
El pFMEA no debería ser algo en solitario
Si se puede evitar este tipo de análisis debería ser realizado por un equipo multidisciplinar. A veces, en las empresas más pequeñas, las personas acaban teniendo que llevar más de un sombrero. Hay muchos empresarios que tienen que funcionar como CEO/CFO/Ingeniero de Diseño/RA/Gerente de QA.
En realidad, se debe utilizar un enfoque de equipo si es factible. Haga que el personal de nivel directivo que tiene la propiedad de los procesos participe en este análisis. Ellos deberían conocer el proceso más íntimamente que cualquier otra persona en la empresa y deberían tener más conocimiento de los posibles modos de fallo de los procesos ya que probablemente los han visto de primera mano. También son el tipo de empleados que conocerían los tipos de acciones recomendadas para controlar el riesgo de esos fallos también.
El pFMEA también debe ser un documento vivo
A medida que se descubren nuevos modos de fallo deben ser añadidos a su pFMEA. Un nuevo modo de falla puede ser descubierto a través de un CAPA porque el proceso tuvo una falla real que no fue analizada originalmente. Tome una instancia como esa como una oportunidad para mejorar y actualizar su pFMEA como parte de un sistema de gestión de riesgos vivo. Además, utilice esto como un momento para volver a pensar en modos de fallo potencialmente similares que pueden no haber sido considerados previamente para que puedan ser controlados antes de que ocurran.
Si se tomó el tiempo de ver el video anterior también se menciona que en algunos casos el primer FMEA debe basarse en estimaciones porque no hay datos. Los gestores e ingenieros pueden verse obligados a estimar la probabilidad de ocurrencia. Si ese es el caso, el FMEA debe ser actualizado en el futuro para ajustar la puntuación (O) para reflejar lo que está ocurriendo en la actualidad sobre la base de datos reales y no los datos teóricos que se utilizaron para la estimación inicial.
Deja una respuesta