Parte 1 de 6: Los fundamentos del polietileno
On noviembre 17, 2021 by adminEl polietileno se comercializa desde hace 80 años. Con todo ese tiempo para ganar experiencia, se podría esperar que hubiéramos aprendido todo lo que hay que saber sobre esta familia de materiales. Sin embargo, a juzgar por las conversaciones que tengo con la gente sobre la selección del PE correcto para una aplicación, la industria tiene mucho que aprender.
El polietileno se considera un material «básico», una designación que da la impresión de que no hay que pensar mucho para elegir el grado correcto del material. Pero el PE puede ser notablemente complicado simplemente porque es el único polímero que está disponible en una amplia gama de densidades.
La densidad suele ser una propiedad inherente. Todos los policarbonatos tienen una densidad de 1,19-1,20 g/cm3, todos los polipropilenos cubren un rango muy estrecho de 0,898-0,905 g/cm3, y la densidad del poliéster PBT es de 1,31 g/cm3. Es posible alterar la densidad de cualquier material, pero estos ajustes implican cambios en la composición. La adición de plastificantes reducirá la densidad del PVC, la mayoría de los modificadores de impacto reducirán la densidad de la resina base a la que se añaden, y las cargas y el refuerzo normalmente aumentarán la densidad de un material.
Pero el PE puede fabricarse con densidades que cubren un rango de 0,86-0,97 g/cm3 sin alterar un ápice la composición molecular. Y a través de este rango el polímero puede presentar una amplia gama de propiedades.
No siempre fue así. El polietileno, como muchos de los polímeros de los que hoy dependemos comercialmente, se creó por accidente. Los investigadores que experimentaban con gases a alta presión descubrieron que cuando realizaban experimentos con el gas etileno, obtenían un compuesto sólido que era el resultado de la polimerización de la molécula de etileno. Se tardó unos seis años en comercializar el material y, según los estándares actuales, el proceso de polimerización era tosco y producía una gama muy reducida de productos.
Hoy llamamos a estos materiales polietileno de baja densidad (LDPE). Pero esta nomenclatura no existía en aquel momento porque no existía el polietileno de alta densidad ni se entendía que tal material pudiera ser siquiera posible. Hace tiempo que sabemos que el PEBD está formado por cadenas que contienen una gran cantidad de ramificaciones. Las largas ramificaciones impiden que los eslabones de la cadena se agrupen estrechamente. Esto limita la capacidad del material para cristalizar y reduce las atracciones intermoleculares que son responsables de proporcionar propiedades de carga como la resistencia y la rigidez.
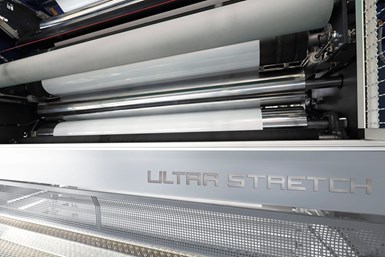
Los continuos desarrollos en el PE han permitido a los procesadores diseñar películas más finas y fuertes que nunca. (Fuente: Reifenhauser)
El uso inicial del PE era como aislante para alambres y cables, por lo que la flexibilidad del PEBD era un atributo positivo. Sin embargo, si intentáramos fabricar un producto como un cubo de 5 galones de PEBD, llenarlo con 40-60 libras de contenido y luego apilar los contenedores llenos a tres o cuatro alturas, se colapsarían rápidamente. Así que, comprensiblemente, las aplicaciones del PE fueron algo limitadas durante los años 40 y hasta mediados de los 50.
Entran Karl Ziegler y Guilio Natta. En 1954, trabajando de forma independiente y algo competitiva, descubrieron catalizadores que permitían la polimerización del etileno sin las temperaturas y presiones extremas que se necesitaban anteriormente. Y lo que es más importante, la molécula resultante carecía en gran medida de las ramificaciones que caracterizaban los resultados de los procesos a alta presión. Estas moléculas lineales podían empaquetarse más juntas creando un conjunto de propiedades muy diferentes. El polietileno de alta densidad (HDPE) era más fuerte, más rígido y más duro, todas ellas consecuencias del mayor grado de cristalinidad que surgía de la disposición más regular de las cadenas poliméricas lineales. También era menos resistente al impacto, especialmente a bajas temperaturas. Pero la mayor resistencia y rigidez del material hizo posible productos como esos cubos de 5 galones.
Dos investigadores de Phillips Petroleum habían descubierto un proceso similar aproximadamente un año antes que Ziegler y Natta, y este sistema para polimerizar el PE se conoce todavía hoy como proceso Phillips. Sin embargo, el logro técnico se convirtió en objeto de un largo y prolongado litigio que no se resolvió hasta la década de 1980, y para entonces la designación de Ziegler-Natta había arraigado firmemente y compartieron el Premio Nobel de Química en 1963 por su logro.
Una vez que se conocieron estos catalizadores de metales de transición, el mundo del polietileno se expandió rápidamente. Se pudo fabricar una amplia gama de densidades, desde 0,91 hasta 0,97 g/cm3, con una amplia gama de propiedades correspondiente. Otros avances produjeron el polietileno lineal de baja densidad (LLDPE) a finales de la década de 1970. Este material introdujo la ramificación de forma más controlada de lo que era posible en el PEBD tradicional.
Aproximadamente en esta misma época se estaba iniciando una nueva revolución en los catalizadores que tendría consecuencias de gran alcance para el polietileno. En 1977, Walter Kaminsky, de la Universidad de Hamburgo, demostró la utilidad de los catalizadores de metaloceno para polimerizar el PE. El camino del desarrollo de estos materiales ha sido largo y tortuoso, pero a finales de los años 90 y en las dos primeras décadas del nuevo milenio, los PE fabricados con estos nuevos sistemas catalizadores añadieron formas del material que antes eran imposibles. El LLDPE catalizado con metaloceno es más difícil de procesar que el LLDPE Ziegler-Natta, al igual que las primeras versiones del LLDPE eran más difíciles que el LDPE tradicional. Pero a medida que los procesadores se pusieron al día con estos materiales, las mejoras en el rendimiento se hicieron evidentes. Las películas podían reducirse sustancialmente, pero produciendo estructuras con un rendimiento equivalente. Se mejoró la claridad, la resistencia al impacto de los dardos y la resistencia al desgarro.
El mayor nivel de control sobre la polimerización que ofrecían estos catalizadores dio lugar a un nuevo conjunto de materiales de polietileno con densidades tan bajas como 0,86 g/cm3. Los bajos niveles de cristalinidad produjeron una familia de materiales denominados plastómeros: materiales flexibles y resistentes que podían duplicar las propiedades de materiales como el copolímero de etileno-acetato de vinilo (EVA) a densidades mucho más bajas y con niveles mejorados de estabilidad térmica en la fusión.
Con todo este desarrollo, la tarea de seleccionar el PE adecuado para una aplicación se ha vuelto cada vez más complicada. La selección del grado correcto de PE siempre ha sido más difícil que la de otras resinas, precisamente por la inusual versatilidad del polímero. En la mayoría de las familias de polímeros, los grados no rellenos y no modificados se distinguen principalmente por su peso molecular. Los grados de mayor peso molecular rinden más, pero son más difíciles de procesar debido a sus mayores viscosidades de fusión. En general, el peso molecular del PE se recoge en la especificación del índice de fluidez o del índice de fusión.
Pero con el PE hay otra propiedad que debe considerarse al definir el rendimiento del material: la densidad. La posibilidad de especificar dos propiedades en lugar de una proporciona una mayor variedad, pero también hace más difícil llegar a una selección adecuada. La persona que selecciona el material debe entender cómo cambian las propiedades en función tanto del peso molecular como de la densidad. (La distribución del peso molecular es otro factor que debe tenerse en cuenta, pero lo trataremos más adelante).
En nuestra próxima columna definiremos la interacción entre el peso molecular y la densidad y, a continuación, ilustraremos la importancia de saber cómo seleccionar los grados de PE en función de estos dos parámetros interrelacionados pero, en última instancia, independientes.
Acerca del autor
Mike Sepe
Mike Sepe es un consultor independiente y global de materiales y procesamiento cuya empresa, Michael P. Sepe, LLC, tiene su sede en Sedona, Arizona. Cuenta con más de 40 años de experiencia en la industria del plástico y ayuda a sus clientes en la selección de materiales, el diseño para la fabricación, la optimización de procesos, la resolución de problemas y el análisis de fallos. Contacto: (928) 203-0408 – [email protected].
CONTENIDO RELACIONADO
-
Pruebas de velocidad de flujo de fusión – Parte 2
Para apreciar plenamente los puntos fuertes y débiles de la prueba de velocidad de flujo de fusión (MFR).de flujo de fusión (MFR) es importante saber algo sobre la forma en que se realiza la prueba.
-
¿Está lleno de vidrio o reforzado con vidrio?
Aquí se explica la diferencia.
-
¿Cómo le gusta el acetal: homopolímero o copolímero?
Los materiales de acetal han sido una opción comercial durante más de 50 años.
Deja una respuesta