Was ist eine pFMEA? (d.h. Prozess-Fehlermöglichkeits- und Einflussanalyse) Medical Device Academy
On Januar 4, 2022 by adminWas ist eine pFMEA? (d.h. Prozess-Fehlermöglichkeits- und -Einfluss-Analyse)
Geschrieben von Matthew Walker am 6. September 2019
Dieser Artikel erklärt, was eine pFMEA ist (d.h. Prozess-Fehlermöglichkeits- und -Einfluss-Analyse) und wie man sie als Teil des Risikomanagementprozesses einsetzt.
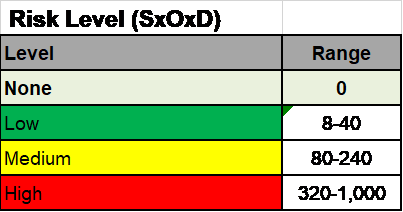
Kürzlich hat mich jemand um Hilfe gebeten, um die Prozess-Fehlermöglichkeits- und -Einfluss-Analyse (pFMEA) besser zu verstehen. Ich kann es ihm nicht verübeln, denn als ich das erste Mal versucht habe, ein entsprechendes Formular auszufüllen, war ich ratlos. Es kann verwirrend und überwältigend sein, wenn man noch nie eine erstellt hat.
Zunächst einmal, was ist eine pFMEA
FMEA= Fehler- und Wirkungsanalyse
Ein Kleinbuchstabe steht vor der FMEA und bezeichnet das „was“, also den Fehler, der analysiert wird. Eine pFMEA wird oft Prozessfehler untersuchen, während eine dFMEA Konstruktionsfehler bewerten könnte. (dFMEAs können auch verwirrend sein, Robert Packard hat in seinem Webinar „Death of the dFMEA“ eine Schulung zur Dokumentation von Risikomanagement-Aktivitäten ohne dFMEA erstellt)
Bei manchen Systemen werden alle Buchstaben groß geschrieben. Manche schreiben keinen groß. Das ist nicht wichtig, solange es im gesamten System konsistent ist. Jeder sollte in der Lage sein, leicht zu verstehen, dass, egal welche Variante von pfmea verwendet wird, es „Prozess-Fehlermodi und -Effektanalyse“ bedeutet.
Was macht eine pFMEA?
Eine pFMEA zerlegt Ihren Fertigungsprozess in seine einzelnen Schritte und untersucht diese methodisch auf mögliche Risiken oder Fehler. Für Unternehmen, die unser Turn-Key-Qualitätsmanagementsystem nutzen, kann die FRM-025-Prozessfehler- und -Einflussanalyse als Vorlage verwendet werden.
In diesem Beispiel betrachten wir die Eingangsprüfung von spritzgegossenen Gehäuseteilen für ein medizinisches Gerät. Diese Eingangsprüfung umfasst eine manuelle Prüfung von 10 zufällig ausgewählten Teilen aus jeder Lieferung von 100 Teilen unter Verwendung eines optischen Overlays.
Prozessschritt
Dieser Bereich ist, wie der Titel des Abschnitts schon sagt, der Prozessschritt. Wenn man den Prozess als Ganzes betrachtet, wird die pFMEA ihn in jeden einzelnen Schritt aufschlüsseln, der zu diesem Prozess gehört. Dieser Bereich ist einfach der einzelne Schritt, der untersucht wird.
Der Prozessschritt oder die Elementfunktion, je nachdem, was Ihr Formular für dieses Szenario verwendet, wird Teil der Stichprobe für die manuelle Prüfung der erhaltenen Teile unter Verwendung eines optischen Overlays sein. Unser Beispiel ist das Beleuchtungselement des optischen Overlay-Displays. Das Beleuchtungselement beleuchtet das geprüfte Teil im Vergleich zur Vorlage, um zu überprüfen, ob das Teil innerhalb bestimmter Abmessungskriterien liegt.
Potenzielle Fehlermodi
Ein Fehlermodus ist eine Art und Weise, in der dieser Prozessschritt fehlschlagen könnte. Da es sich um eine Ausfallart handelt, muss berücksichtigt werden, dass es mehr als eine Möglichkeit geben kann, wie der Prozessschritt ausfallen kann. Lassen Sie sich nicht davon täuschen, dass die pFMEA vollständig ist, nur weil dieses Feld auf dem Formular ausgefüllt wurde. Es sollte eine gründliche Untersuchung aller möglichen Ausfälle durchgeführt werden.
Unser Beispiel in diesem Prozess erfordert das Beleuchtungselement, um eine visuelle Vorlage über den Teilen zu beleuchten. Wenn das Licht nicht richtig leuchtet, ist das ein möglicher Fehler in diesem Prozess.
Potenzielle Auswirkungen eines Fehlers
Die potenziellen Auswirkungen eines Fehlers sind ein Blick auf die Folgen, die eintreten würden, wenn der Fehler in diesem Prozessschritt tatsächlich auftritt.
In unserem Szenario besteht eine der potenziellen Auswirkungen einer nicht ordnungsgemäß funktionierenden Beleuchtung darin, dass Teile, die nicht den festgelegten Größenakzeptanzkriterien entsprechen, möglicherweise akzeptiert werden, anstatt sie als nicht konforme Teile zurückzuweisen.
S (Schweregrad)
Der nächste Bereich ist der erste Bereich, der eine geschätzte Einstufung des Fehlers erfordert. Das ist der „Schweregrad“, der mit S abgekürzt wird. Im Abschnitt über die Einstufung im FRM-025 ist eine Skala enthalten, die das von der Medical Device Academy verwendete Nummerierungssystem beschreibt.
Nachfolgend finden Sie einen Auszug aus der verwendeten Bewertungsskala, die beim Kauf des Risikomanagementverfahrens SYS-010 enthalten ist.
Schweregrad (S) | ||
Schwere der Auswirkung | Skala | Definition |
Geschäftsrisiko | 0 | Kein potenzieller Schaden für Patient oder Anwender |
Oberflächlich | 2 | Geringes Potenzial für Schaden für Patient oder Anwender |
In diesem Fall, In diesem Fall handelt es sich um geformte Kunststoffteile des Außengehäuses eines Medizinprodukts. Zu große oder zu kleine Teile werden bei der Endmontage des Geräts nicht passen. Diese Kunststoffteile kommen nicht mit dem Patienten in Berührung und beeinträchtigen die Funktion des Geräts nicht.
Bei der Bewertung dieses Fehlers wird festgestellt, dass er keine potenziellen Auswirkungen auf die Patientensicherheit hat oder ein potenzielles Schadensrisiko erhöht, daher wird der Schweregrad als „Geschäftsrisiko“ eingestuft, was bedeutet, dass er kein Risiko für den Anwender oder den Patienten darstellt. Damit ist der Schweregrad 0.
Fehlerursachen
Diese Spalte ist genau das. Was könnte die Ursache für diese festgestellte Störung sein? In unserem Beispiel könnten die Glühbirnen in der Overlay-Maschine mit der Zeit durchbrennen. Dieses Durchbrennen verursacht einen möglichen Ausfall.
Wenn man davon ausgeht, dass die Glühbirne nur eine Lebensdauer von 100 Stunden hat, dann wird das Licht mit zunehmender Nutzungsdauer immer schwächer. Ein langsam abdunkelndes Licht verringert die Schärfe der Überlagerungsvorlage, und unsere Teile, die ein + oder – Größenkriterium von 10 % haben sollten, haben nun eine unscharfe Vorlage, die in Wirklichkeit die Überlagerung so verändert, dass sie näher an + oder – 13 % liegt. Jetzt können Teile, die zu klein oder zu groß sind, akzeptiert werden.
O (Auftreten/Wahrscheinlichkeit)
Dieses Einstufungskriterium findet sich auch im Abschnitt „Bewertung“ des FRM-025. Es gibt an, wie oft der Fehler voraussichtlich auftreten wird. Wie oft wird das Beleuchtungselement unseres optischen Overlays aus diesem Grund nicht richtig funktionieren?
Hoffentlich nicht sehr oft. Eine regelmäßige Wartung und Kalibrierung der Overlay-Maschine könnte im besten Fall verhindern, dass dies jemals passiert. Unsere Auswertungen haben ergeben, dass die Wahrscheinlichkeit, dass dies geschieht, gering ist. Da wir jedoch nicht sicher sein können, dass es nie passiert, besteht das Potenzial für dieses Risiko, so dass der Wert für das Auftreten bei 4 liegt.
Gegenwärtige Prozesskontrollen
Was wird gegenwärtig zur Kontrolle dieses Risikos getan? In unserem Beispiel werden regelmäßige Wartungs- und Kalibrierungsarbeiten durchgeführt, um zu verhindern, dass das Durchbrennen der Glühbirne das Overlay beeinträchtigt.
D (Nachweisbarkeit)
Unser derzeitiger Prozess basiert auf routinemäßiger Wartung und Sichtprüfung. Das bedeutet, dass das Durchbrennen der Glühbirne visuell überprüft wird und die visuelle Überprüfung der Erkennbarkeit auf der Bewertungsskala mit 8 bewertet wird. Diese Tabelle ist im Abschnitt Bewertung des FRM-025 zu finden.
RPN (Risikoprioritätszahl)
Diese Zahl ergibt sich aus der Multiplikation von Schweregrad, Wahrscheinlichkeit und Entdeckbarkeit. In unserem Beispiel ist die RPZ 0X4X8=32 für eine RPZ von 32, was als NIEDRIG gilt.
pFMEA-Mathematik
Unten finden Sie ein kurzes Video, in dem die Mathematik hinter der Berechnung der Risikoprioritätszahl erklärt wird
Empfohlene Maßnahmen
Was kann man tun, um diesen Prozess zu verbessern? In unserem Beispiel könnte eine empfohlene Maßnahme darin bestehen, von reinen Sichtkontrollen zur Überprüfung der Lichtleistung durch das Messgerät überzugehen. Dadurch wird die Erkennbarkeit des Fehlers durch ein Messgerät oder eine Lehre messbar, was einem Erkennbarkeitswert von 4 entspricht.
Dadurch ändert sich die RPZ jetzt auf 0X4X4=16
Die pFMEA sollte nicht im Alleingang durchgeführt werden
Wenn es sich vermeiden lässt, sollte diese Art von Analyse von einem multidisziplinären Team durchgeführt werden. In kleineren Unternehmen gibt es manchmal Leute, die mehr als einen Hut tragen müssen. Es gibt viele Unternehmer, die als CEO/CFO/Konstrukteur/RA/QA-Manager fungieren müssen.
In der Regel sollte ein Teamansatz verfolgt werden, wenn dies möglich ist. Lassen Sie die Mitarbeiter der Managementebene, die für die Prozesse verantwortlich sind, an dieser Analyse teilnehmen. Sie kennen den Prozess besser als jeder andere im Unternehmen und haben einen besseren Einblick in die möglichen Fehlerarten der Prozesse, da sie diese wahrscheinlich aus erster Hand kennen. Sie sind auch die Art von Mitarbeitern, die die Arten von empfohlenen Maßnahmen kennen, um das Risiko dieser Fehler zu kontrollieren.
Die pFMEA sollte auch ein lebendiges Dokument sein
Wenn neue Fehlermöglichkeiten entdeckt werden, sollten sie zu Ihrer pFMEA hinzugefügt werden. Ein neuer Fehlermodus könnte durch eine CAPA entdeckt werden, weil der Prozess einen tatsächlichen Fehler hatte, der ursprünglich nicht analysiert wurde. Nehmen Sie einen solchen Fall als Gelegenheit zur Verbesserung und zur Aktualisierung Ihrer pFMEA als Teil eines lebendigen, atmenden Risikomanagementsystems. Nutzen Sie dies auch als Gelegenheit, um über potenziell ähnliche Fehlermöglichkeiten nachzudenken, die zuvor nicht berücksichtigt wurden, damit sie kontrolliert werden können, bevor sie auftreten.
Wenn Sie sich die Zeit genommen haben, das obige Video anzuschauen, wird auch erwähnt, dass in manchen Fällen die allererste FMEA auf Schätzungen beruhen muss, weil es keine Daten gibt. Manager und Ingenieure können gezwungen sein, die Wahrscheinlichkeit des Auftretens zu schätzen. Wenn dies der Fall ist, sollte die FMEA in der Zukunft aktualisiert werden, um die (O)-Punktzahl so anzupassen, dass sie das widerspiegelt, was tatsächlich auf der Grundlage realer Daten und nicht der theoretischen Daten, die für die erste Schätzung verwendet wurden, auftritt.
Schreibe einen Kommentar