Die Leistungsfähigkeit des Drahterodierens
On Januar 8, 2022 by admin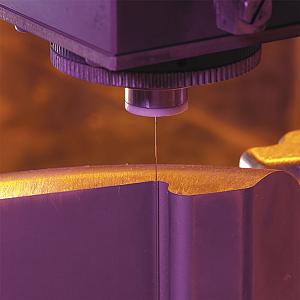
Foto mit freundlicher Genehmigung von Makino.
Das Drahterodieren (EDM) gibt es schon seit Jahrzehnten, aber diese Technologie hat andere Bearbeitungsverfahren in der Werkstatt nie in den Schatten gestellt. Das liegt daran, dass die Funkenerosion einen interessanten Mehrwert bietet – sie ist in der Lage, jedes Teil zu schneiden, das leitfähig ist, unabhängig von seiner Härte, wo konventionelle Metallabtragung schwierig oder unmöglich ist, aber der Prozess selbst ist schrittweise. Experten sind sich einig, dass die Werkstätten immer etwas zögerlich waren, wenn es um die Einführung dieser Technologie ging.
„EDM hatte das Stigma, eine schwarze Kunst zu sein“, sagte Brian Pfluger, EDM-Produktlinienmanager bei Makino, Mason, Ohio. „Geschäfte mit wenig oder gar keiner Erfahrung waren nicht bereit, diese Technologie zu erforschen, aber in letzter Zeit hat sich das geändert.“
„Obwohl das Drahterodieren nur einen kleinen Marktanteil hat, hat es definitiv seinen Platz“, sagte Steve Raucci, EDM Produktmanager, Methods Machine Tools, Inc. „Die Luft- und Raumfahrt und die Medizintechnik sind einige der Industriezweige, die EDM einsetzen, aber auch die Feuerwaffenindustrie ist ein großer Akteur auf dem EDM-Markt. Die Funkenerosion ist ein langsamer Prozess, aber es gibt immer noch Teile, die mit einem Draht hergestellt werden müssen. Manchmal gibt es keine andere Möglichkeit.“
Die Hersteller haben sich darauf konzentriert, wie klein und fein das EDM-Verfahren sein kann. In den letzten Jahren hat das Verfahren jedoch eine Art Plateau erreicht. Es gab einige Bereiche, in denen Verbesserungen erzielt wurden. So argumentierten die Experten, dass noch vor 10 Jahren sicherheitskritische Bauteile für die Luft- und Raumfahrt niemals auf einer Erodiermaschine hergestellt worden wären. Die Stromversorgungen und Drähte wurden jedoch so angepasst, dass Teile ohne Nachguss und mit unterschiedlichen Materialstärken problemlos hergestellt werden können.
„Wenn Sie scharfe Ecken oder tiefe Rippen herstellen müssen, die mit einem herkömmlichen Fräswerkzeug nicht erreicht werden können, ist das Drahterodieren eine großartige Option“, sagte Sean Smith, Vertriebsleiter Kanada bei GF Machining Solutions in Mississauga, Ont. „Diese Maschinen sind vielseitig einsetzbar, und wir sehen einen besonderen Bedarf in Bereichen, in denen die Werkstoffe härter werden und einen hohen Nickelgehalt aufweisen, was eine erhöhte Belastung für Werkzeuge und Spindeln bedeutet. Das Erodieren ist für diese Anwendungen perfekt geeignet.“
Das Erodieren hat sich einen einzigartigen Marktanteil erobert, und obwohl bestimmte Merkmale nicht mehr so stark ausgeprägt sind, hat sich eine Entwicklung bei der Größe des Arbeitsraums vollzogen.
„In den Branchen, in denen das Erodieren zum Einsatz kommt, beobachten wir eine Zunahme der Teilegröße“, so Evan Syverson, Additive und HSM Business Manager, Sodick Inc. in Schaumburg, Illinois. „Das hat wirklich begonnen, einige der Spezifikationen und das Design dieser Maschinen zu beeinflussen. Die Grundfläche der Maschinen wächst als Reaktion auf die Art der Arbeiten, die wir sehen, insbesondere in der Z-Achse.“
EDMS FÜR DIE ADDITIVE FERTIGUNG
Außerhalb der traditionellen Sektoren ist die additive Fertigung von Metallen (AM) eine neue Marktchance für das Erodieren. Die meisten Hersteller bieten eine Reihe von Erodiermaschinen an, von einfachen Modellen bis hin zu Spitzenmaschinen mit allem Drum und Dran. Maschinen, die für 3D-gedruckte Metallteile konzipiert sind, haben jedoch eine sehr spezifische Funktion.
„3D-Teile aus Metall werden auf einer Grundplatte hergestellt, die entfernt werden muss“, erklärt Syverson. „Wenn ein Teil gedruckt wird, hat es in der Regel einen relativ großen XY-Achsenweg, aber um es von der Platte zu entfernen, muss es neu ausgerichtet werden, damit es aufrecht steht und mit einer Drahterodiermaschine abgetrennt werden kann.“
Diese Maschinen benötigen eine relativ hohe Z-Achse, um die Teile aufnehmen zu können, und müssen nicht in der Lage sein, mehrere Teiledurchgänge durchzuführen oder eine superhohe Präzision zu erzeugen. Das Erodieren von 3D-gedruckten Teilen erfordert eine allgemeine Geschwindigkeit und die grundlegende Fähigkeit, ein Teil von der Grundplatte zu entfernen. Mit der zunehmenden Verbreitung von AM konzentrieren sich immer mehr Hersteller auf die Bereitstellung von Maschinen für dieses Marktsegment.
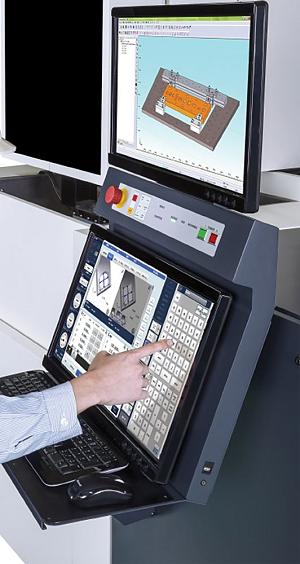
Die neuesten intuitiven Steuerungen ermöglichen es selbst dem unerfahrensten Bediener, sehr präzise und fachmännische Einstellungen an der Maschine vorzunehmen, ohne dass er die zugrunde liegende Technologie kennen muss. Foto mit freundlicher Genehmigung von Makino.
BEDIENUNGSTECHNIK
Die Hersteller dieser Technologie haben das System so angepasst, dass es einfach zu bedienen ist, und räumen mit der Vorstellung auf, dass es sich beim Erodieren um eine Art „schwarze Magie“ handelt, die nur Experten auf diesem Gebiet bedienen können.
„Die Modernisierung der Steuersysteme hat dazu beigetragen, die Angst vor dem Unbekannten zu beseitigen, bei dem die Bediener nicht die falschen Knöpfe drücken wollen oder nicht wissen, wie sie mit der Maschine umgehen sollen“, so Pfluger.
Die neuesten intuitiven Steuerungen ermöglichen es selbst dem unerfahrensten Bediener, sehr präzise und fachmännische Einstellungen an der Maschine vorzunehmen, ohne dass er die zugrunde liegende Technologie kennen muss. Grafische Schnittstellen mit zahlreichen adaptiven Steuerelementen machen es dem Bediener leicht, die Parameter an die jeweilige Aufgabe anzupassen. Dies ist besonders wichtig, da es oft schwierig ist, qualifizierte Bediener zu finden, die bereits Erfahrung mit dem Erodieren haben.
„Die Steuerungen und die Technologie sind einfacher und leichter zu bedienen als noch vor 10 Jahren“, so Raucci. „Über die Schnittstelle kann der Bediener den Drahtdurchmesser, die Materialstärke usw. auswählen. Die Maschine errechnet dann die erforderlichen Schneidparameter, um den Auftrag zu erledigen. Raucci fügte hinzu, dass dies eine erhebliche Verbesserung in den letzten Jahren darstellt. Als er in der Branche anfing, waren die Schneidparameter in Handbüchern zu finden, und wenn das, wonach ein Bediener suchte, nicht enthalten war, musste er mit den Spezifikationen herumspielen, um die richtigen Optionen zu erhalten.
„Jetzt muss man nur noch die Größe des Werkstücks, die gewünschte Toleranz und die gewünschte Oberflächenqualität zusammen mit dem gewählten Draht kennen“, sagte Smith. „Jetzt ist es ganz einfach, die Felder auf der Steuerung auszufüllen.
Die Maschinen sind auch mit Funktionen ausgestattet, die zur Produktivitätssteigerung beitragen. Die Hersteller haben erkannt, dass das Hinzufügen eines Sparmodus oder von Energiesparoptionen für Benutzer von Vorteil ist, die die Maschine bei Dunkelheit betreiben.
Smith nennt das Beispiel eines Wochenendauftrags, bei dem es nicht eilig ist, das Teil so schnell wie möglich fertigzustellen. Funktionen wie der Sparmodus reduzieren die Betriebsparameter und sparen so Kabel und Strom. Anstatt also ein Teil am Samstagnachmittag bei vollen Betriebskosten fertigzustellen, kann das Teil einige Stunden später fertiggestellt werden, wenn die Maschine im Energiesparmodus läuft.
Der Draht
„Einer der großen Fortschritte auf dem Markt ist heutzutage die Möglichkeit, den Draht in den Spalt einzufädeln“, so Pfluger. Wenn ein Draht reißt, was durchaus vorkommen kann, ermöglicht diese Funktion das erneute Einfädeln des Drahts direkt an der Bruchstelle, anstatt den ganzen Weg zurück zum Anfang gehen zu müssen.
„Ohne ein Brucherkennungssystem könnte man fast keine Lights-Out-Operationen durchführen“, so Syverson.
Die Hersteller konzentrieren sich auf die Entwicklung fortschrittlicher Drahteinfädler, die die Produktivität erhöhen, eine höhere Zuverlässigkeit bieten und die Teileverarbeitung verbessern. Ein System, das auch Drahtbrüche erkennt und den Bediener warnt, macht es einfacher, die Maschine wieder in Gang zu bringen und effizient zu betreiben.
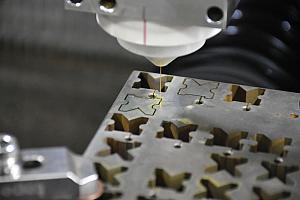
Die Butzenrückhaltung verhindert, dass Butzen herunterfallen und macht Klemmen überflüssig. Ein automatisches Drahtvorschubsystem kann durch die Schnittfuge einfädeln, was die volle Nutzung dieser Funktion ermöglicht. Foto mit freundlicher Genehmigung von Methods Machine Tools.
Drahteinfädler und Brucherkennungssysteme sind wichtige Komponenten, aber Pfluger erklärte, dass einer der größten Kostenfaktoren beim Maschinenbetrieb, neben der Bezahlung des Bedieners für den Betrieb der Maschine, der Draht selbst ist. Immer mehr Hersteller konzentrieren sich auf die Entwicklung effizienterer Maschineneinstellungen, die bei gleichbleibender Teilequalität weniger Draht verbrauchen.
Dies hat dazu geführt, dass viele Hersteller jetzt Großdrahttechnologie anbieten. Pfluger erläuterte, dass der gebräuchlichste Draht einen Durchmesser von 0,25 mm hat, dass aber immer mehr Anwender einen Draht mit größerem Durchmesser, z. B. 0,3 mm, verwenden, weil dies Geschwindigkeitsvorteile bietet. Im Allgemeinen gilt: Je schneller die Maschine arbeitet, desto mehr muss der Bediener bei der Verwendung von Drähten mit größerem Durchmesser auf die Oberflächengüte und Genauigkeit herkömmlicher Drahtgrößen verzichten. Die Hersteller entwickeln jedoch optimierte Einstellungen für die Maschine, die mit dem größeren Durchmesser die gleiche Oberflächengüte und Genauigkeit wie mit herkömmlichem Draht erzielen. Dies ermöglicht Zykluszeiteinsparungen von bis zu 20 Prozent, insbesondere bei Schruppschnitten. Außerdem wird der Drahtverbrauch gesenkt, was zu erheblichen Kosteneinsparungen führt.
Beleuchtete Arbeitsgänge
Das Drahterodieren hat einige eingebaute Beschränkungen und Maschinenvariablen, die eine Automatisierung schwierig machen, weshalb die Roboterautomatisierung bei dieser Technologie nie ein gängiger Trend war. Aber die Experten sind sich einig, dass immer mehr Kunden nach Möglichkeiten zur Automatisierung des Prozesses fragen.
„Wir sehen immer mehr Erodierzellen mit spezieller Automatisierung“, sagt Raucci. „Vor zehn Jahren gab es so etwas noch nicht. Die Zellen verfügen in der Regel über mehrere Erodiermaschinen mit automatisierten Schienensystemen. Dieser Trend wird immer beliebter, weil die Arbeitskosten gestiegen sind und es an qualifiziertem Personal mangelt.“
Raucci stellte fest, dass es immer noch eine große Kluft bei den Kundenwünschen gibt. Er sagte, dass einige die Standardmaschine mit nur einem Bediener bevorzugen, während andere die volle Funktionalität mit Lights-Out nutzen wollen. Dazu könnte ein Drehtisch mit zusätzlicher Automatisierung und ein Messtaster gehören. Durch die Integration eines Messtasters wird die Qualität der Teile sichergestellt, was für jeden, der einen Lights-Out-Betrieb anstrebt, äußerst vorteilhaft sein kann.
„Die Hinzufügung von Automatisierung ist definitiv eine Möglichkeit für Kunden, auf dem Markt wettbewerbsfähiger zu sein“, fügt Smith hinzu. „Sie können von einem einfachen Palettenwechselsystem bis hin zu mehrachsigen Robotern gehen, die bei der Beladung der Maschinen helfen.“
Die Experten waren sich einig, dass Automatisierung und Lights-Out-Betrieb den Einstieg in die Technologie für die Betriebe erleichtern. Smith gab jedoch zu bedenken, dass Betriebe, die eine Roboterzelle einbauen wollen, auch sicherstellen müssen, dass sie immer genügend Draht zur Verfügung haben, um die Vorteile der Technologie voll nutzen zu können. In den meisten Fällen können die heutigen Maschinen etwa 55 Pfund Draht fassen, was etwa 80 Stunden unbeaufsichtigte Schneidzeit und Energie ergibt.
„Die Technologie selbst hat sich im Laufe der Jahre stark weiterentwickelt“, sagte Syverson. „Wenn ein Bediener die Steuerungen und die integrierte Programmiersoftware bedienen kann, läuft die Maschine im Wesentlichen von selbst. Und jetzt, mit der Automatisierung, gibt es mehr Möglichkeiten als je zuvor für die Werkstätten, die einzigartigen Fähigkeiten des Erodierens zu nutzen.“
Assoziierte Redakteurin Lindsay Luminoso ist erreichbar unter [email protected].
GF Machining Solutions, www.gfms.com
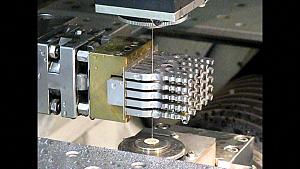
„Einer der großen Vorstöße auf dem Markt ist heutzutage die Fähigkeit, den Draht in den Spalt einzufädeln“, sagte Brian Pfluger. Foto mit freundlicher Genehmigung von Makino.
Makino, www.makino.com
Methods Machine Tools, www.methodsmachine.com
Sodick, www.sodick.com
Schreibe einen Kommentar