Pochopení síly elektroerozivního obrábění drátem
On 8 ledna, 2022 by admin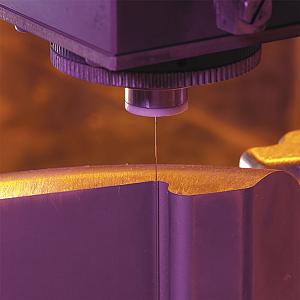
Foto s laskavým svolením společnosti Makino.
Elektroerozivní obrábění drátem (EDM) existuje již desítky let, přesto tato technologie nikdy nezastínila ostatní obráběcí procesy v dílně. Je to proto, že elektroerozivní obrábění nabízí zajímavou hodnotu – je schopno řezat jakýkoli díl, který je vodivý, bez ohledu na jeho tvrdost, kde je konvenční úběr kovu náročný nebo nemožný, ale samotný proces je postupný. Odborníci se shodují na tom, že obchody měly vždy poněkud obavy, pokud jde o zavádění této technologie.
„EDM mělo stigma černého umění,“ řekl Brian Pfluger, manažer produktové řady EDM, Makino, Mason, Ohio. „Dílny s malými nebo žádnými zkušenostmi nebyly ochotny tuto technologii zkoumat, ale v poslední době určitě došlo k posunu.“
„Přestože si elektroerozivní obrábění drátem stále drží jen malý podíl na trhu, rozhodně má své místo,“ řekl Steve Raucci, produktový manažer elektroerozivního obrábění, Methods Machine Tools, Inc. „Letecký a lékařský průmysl jsou některá z průmyslových odvětví, která zavádějí elektroerozivní obrábění, ale dalším velkým hráčem na trhu s elektroerozivním obráběním je zbrojní průmysl. EDM je pomalý proces, ale stále existují díly, které se musí vyrábět pomocí drátu. Někdy to ani jinak nejde.“
Výrobci se zaměřili na to, jak malý a jemný může být proces EDM. V posledních několika letech se však samotný proces dostal do určité roviny. V některých oblastech došlo ke zlepšení. Odborníci například tvrdili, že ještě před 10 lety by se na elektroerozivním obrábění nikdy nevyráběly součásti kritické z hlediska bezpečnosti v leteckém průmyslu. Napájecí zdroje a drát však byly upraveny tak, aby bylo možné snadno vyrábět díly bez přetavování a s různou tloušťkou materiálu.
„Když potřebujete vyrobit ostré rohy nebo hluboká žebra, tedy prvky, do kterých se běžný frézovací nástroj nedostane, je elektroerozivní obrábění skvělou volbou,“ řekl Sean Smith, obchodní manažer pro Kanadu společnosti GF Machining Solutions, Mississauga, Ont. „Tyto stroje jsou univerzální a potřebu vidíme zejména v oblastech, kde se materiály stávají tvrdšími, s vysokým obsahem niklu, což zvyšuje tlak na nástroje a vřetena. Elektroerozivní obrábění je pro tyto aplikace ideální.“
EDM si získalo jedinečný podíl na trhu, a přestože se některé funkce ustálily, jeden vývoj nastal ve velikosti pracovní obálky.
„V průmyslových odvětvích, kterým EDM obvykle slouží, pozorujeme nárůst velikosti dílů,“ řekl Evan Syverson, obchodní manažer pro aditivní a HSM obrábění, Sodick Inc., Schaumburg, Ill. „To skutečně začalo ovlivňovat některé specifikace a konstrukci těchto strojů. Plocha strojů se zvětšuje v reakci na typ práce, který vidíme, zejména v ose Z.“
EDMS PRO ADITIVNÍ VÝROBU
Novou tržní příležitostí pro elektroerozivní obrábění je kromě tradičních odvětví také aditivní výroba kovů (AM). Většina výrobců nabízí řadu EDM strojů, od základních modelů až po špičkové stroje se všemi zvonky a píšťalkami. Stroje určené pro kovové 3D tištěné díly však mají velmi specifickou funkci.
„Kovové 3D díly jsou postaveny na základní desce, kterou je třeba odstranit,“ vysvětlil Syverson. „Když je díl vytištěn, má obvykle poměrně široký pojezd v ose XY, ale aby mohl být z této desky odstraněn, musí být přeorientován, aby mohl být vzpřímen a oddělen pomocí drátového elektroerozivního obrábění.“
Tyto stroje potřebují poměrně vysokou osu Z, aby byly schopny pojmout díly, a nemusí být schopny provádět více průchodů dílu nebo vyrábět super vysokou přesnost. EDM pro 3D tištěné díly vyžaduje obecnou rychlost a základní schopnost vyjmout díl ze základní desky. Stále více výrobců se zaměřuje na poskytování strojů určených pro tento segment trhu, protože AM se stává stále běžnějším.
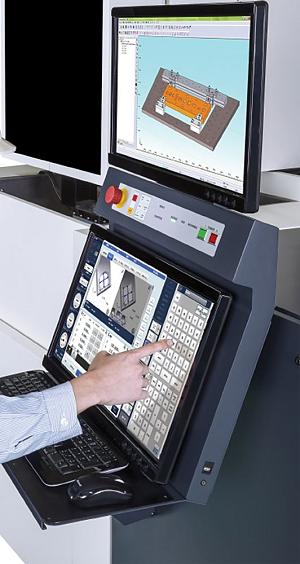
Nejnovější intuitivní ovládání umožňuje i nezkušené obsluze provádět velmi přesná nastavení stroje na úrovni odborníka, aniž by musela znát základní technologii. Foto s laskavým svolením společnosti Makino.
Ovládání
Výrobci této technologie přizpůsobili systém tak, aby se snadno používal, a vyvrátili tak představu, že elektroerozivní obrábění je jakási „černá magie“, kterou mohou ovládat pouze odborníci v oboru.
„Modernizace řídicích systémů pomohla odstranit strach z neznámého, kdy obsluha nechce stisknout nesprávná tlačítka nebo nerozumí tomu, jak se strojem komunikovat,“ řekl Pfluger.
Nejnovější intuitivní ovládání umožňuje i nezkušené obsluze provádět velmi přesná nastavení stroje na úrovni odborníka, aniž by nutně musela znát základní technologii. Grafická rozhraní, která poskytují řadu adaptivních ovládacích prvků, usnadňují obsluze nastavení parametrů tak, aby vyhovovaly dané práci. To je důležité zejména proto, že často může být problém najít kvalifikované operátory, kteří mají předchozí zkušenosti s elektroerozivním obráběním.
„Ovládací prvky a technologie se zjednodušily a snadno se ovládají, než tomu bylo ještě před 10 lety,“ řekl Raucci. „Rozhraní umožňuje obsluze zvolit průměr drátu, tloušťku materiálu atd. Stroj vypočítá řezné parametry potřebné k provedení práce.“ Raucci dodal, že se jedná o výrazné zlepšení za posledních několik let. Když začínal v oboru, řezné parametry se nacházely v manuálech, a pokud to, co operátor hledal, nebylo zahrnuto, musel si se specifikacemi pohrát, aby získal správné možnosti.
„Nyní stačí znát pouze velikost obrobku, toleranci, kterou hledáte, kvalitu povrchu, které se snažíte dosáhnout, spolu s drátem, který si vyberete,“ řekl Smith. „Nyní je to snadné jako vyplnit prázdná políčka na ovládacím panelu. Stroj se o to postará.“
Stroje jsou také vybaveny funkcemi, které pomáhají při zvyšování produktivity. Výrobci si uvědomují, že přidání úsporného režimu nebo možností úspory energie je výhodné pro uživatele, kteří se strojem pracují ve scénářích s vypnutým světlem.
Smith uvádí příklad zakázky prováděné o víkendu, kdy není třeba spěchat, aby byl díl dokončen co nejrychleji. Funkce, jako je úsporný režim, sníží provozní parametry, ušetří dráty a spotřebu energie. Takže místo toho, aby byl díl dokončen v sobotu odpoledne za plných provozních nákladů, může být dokončen o několik hodin později s tím, že stroj poběží v úsporném režimu.“
DRÁT
„Jedním z velkých tlaků na trhu je v dnešní době možnost provlékání drátu v mezeře,“ řekl Pfluger. Když se drát přetrhne, což se může stát, tato schopnost umožňuje znovu navléknout drát přímo v místě přetržení, místo aby se musel vracet až na začátek.
„Téměř byste nemohli mít provoz bez světel, kdyby neměl systém detekce přetržení,“ řekl Syverson.
Výrobci se zaměřují na vývoj pokročilých navlékačů drátu, které zvyšují produktivitu, nabízejí lepší spolehlivost a zlepšují zpracování dílů. Mít systém, který detekuje i přetržení drátu a upozorní obsluhu, usnadňuje opětovné efektivní zprovoznění stroje.
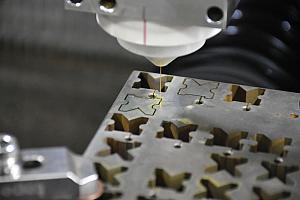
Zadržení závitů zabraňuje vypadávání závitů a eliminuje potřebu svorek. Automatický systém podávání drátu může vést závit přes prořez, což umožňuje plné využití této funkce. Foto s laskavým svolením společnosti Methods Machine Tools.
Závitníky drátu a systémy detekce přerušení jsou důležité komponenty, ale Pfluger vysvětlil, že jedním z největších nákladů na provoz stroje, kromě placení obsluhy za provoz stroje, je samotný drát. Stále více výrobců se zaměřuje na vývoj efektivnějších nastavení strojů, které spotřebují méně drátu při zachování kvality dílů.
To vedlo k tomu, že mnoho výrobců nyní nabízí technologii velkých průměrů drátu. Pfluger například vysvětlil, že nejběžnější drát má průměr 0,25 mm, ale stále více operátorů používá drát s větším průměrem, například s průměrem 0,3 mm, protože nabízí výhody v oblasti rychlosti. Obecně platí, že čím rychleji stroj pracuje, tím více musí operátor při použití drátu o větším průměru obětovat povrchovou úpravu a přesnost výkonu tradičních velikostí drátu. Výrobci však vyvíjejí optimalizovaná nastavení stroje, která poskytují stejnou kvalitu povrchu a přesnost při použití většího rozměru, jakou poskytuje tradiční drát. To umožňuje až dvacetiprocentní úsporu času cyklu, zejména při hrubých řezech. Snižuje se také spotřeba drátu, což vede k výrazné úspoře nákladů.
VÝROBNÍ OPERACE
Drátové elektroerozivní obrábění má některá vestavěná omezení a proměnné stroje, které ztěžují jeho automatizaci, a proto robotická automatizace nikdy nebyla u této technologie běžným trendem. Odborníci se však shodují, že stále více zákazníků se ptá na způsoby automatizace tohoto procesu.
„Vidíme stále více buněk EDM se specializovanou automatizací,“ řekl Raucci. „Před deseti lety nic takového neexistovalo. Buňky mají tendenci mít více EDM strojů s automatizací kolejnicového systému. Tento trend je stále populárnější kvůli zvýšeným nákladům na pracovní sílu a nedostatku kvalifikovaných operátorů.“
Raucci poznamenal, že stále existuje velký rozdíl v tom, co zákazníci hledají. Řekl, že někteří mají rádi standardní stroj s jednou obsluhou, zatímco jiní naskakují s možností plného vypnutí světel. To může zahrnovat otočný stůl s další automatizací a sondou. Začlenění sondy zajišťuje kvalitu dílů, což může být velmi výhodné pro každého, kdo chce provozovat operace lights-out.
„Přidání automatizace je pro zákazníky rozhodně způsob, jak být na trhu konkurenceschopnější,“ dodal Smith. „Mohou přejít od zcela základního systému výměny palet až po víceosé roboty, které pomáhají nakládat stroje.“
Experti se shodli, že automatizace a operace lights-out usnadňují obchodům vstup do této technologie. Smith však upozornil, že obchody, které chtějí začlenit robotickou buňku, musí také zajistit, aby měly vždy dostatečný přívod drátu, aby mohly tuto technologii plně využít. Většinou dnešní stroje pojmou asi 55 liber drátu, což dává přibližně 80 hodin bezobslužného řezání a energie.
„Samotná technologie urazila za ta léta obrovský kus cesty,“ řekl Syverson. „Pokud obsluha umí používat ovládací prvky a palubní programovací software, stroj se v podstatě řídí sám. A nyní, díky automatizaci, existuje více způsobů, jak mohou dílny využívat jedinečné možnosti elektroerozivního obrábění než kdykoli předtím.“
Související redaktorka Lindsay Luminoso je k dispozici na adrese [email protected].
GF Machining Solutions, www.gfms.com
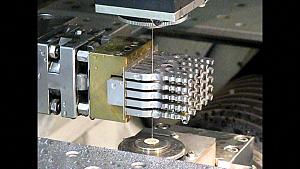
„Jedním z velkých tlaků na trhu je v dnešní době možnost provlékání drátu v mezeře,“ řekl Brian Pfluger. Foto: Makino.
Makino, www.makino.com
Methods Machine Tools, www.methodsmachine.com
Sodick, www.sodick.com
.
Napsat komentář